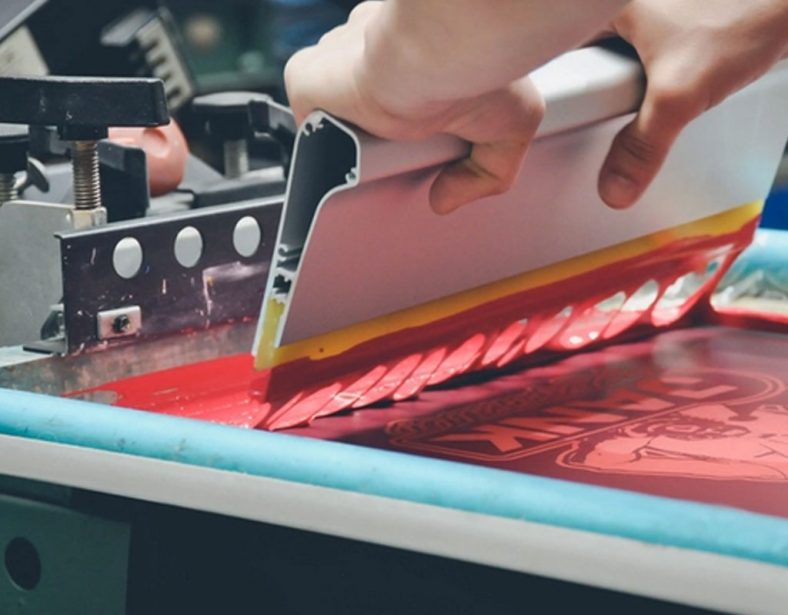
Custom Screen Printing
Screen printing uses a screen cut-out plate and printing material, using a squeegee to get the graphics.
Printing is done by filling one end of the screen printing plate with ink, applying pressure to the ink area with a squeegee while moving evenly towards the other end of the screen, and the ink is squeezed from the mesh holes onto the printed object.
The advantages of screen printing are that the screen can be attached to various shapes of objects, so it is possible to print on curved surfaces, and that screen printing can use a variety of inks and paint mixes, for example light resistant pigments can be mixed into the ink, giving the screen printed product a great advantage in terms of light resistance.
Screen printing is widely used because of its extreme adaptability. Text decorations on surfaces like clothes, shoes, electrical appliances, ceramics, glass and floor tiles are almost always screen printed. And in the field of packaging, screen printing is commonly used for high-grade packaging boxes and bottles, like holiday gift boxes, cigarette boxes and wine boxes.Screen printing includes flat screen printing, cylindrical screen printing, oval screen printing, high volume automatic screen printing & taper screen printing. Multi-color printing can also be performed by changing screens & re-registering parts to be decorated. High volume screen printing capacity is printing up to three colors at a rate of 3000 pieces per hour with labeling. Wonder Plastic is a Lean manufacturing capable custom manufacturer of screen printing. No matter what you’re looking for, we can accommodate nearly any specifications to deliver the plastic film or bags that best suits your application.
-
PE Biodegradable Material PET Poop Bags
-
Transparent Flat Self-Adhesive PE Packaging Bags
-
3-5 Years Old Children’s Socks Packaging Bag
-
PE Organ Shape Bag For Textile Products
-
PE Organ Shape Bag For Clothing
-
Packaging Bag For PET Grooming Glove
-
Medical Packaging Bag For Disposable Respirator
-
Packaging Bag For KN95 Protective Mask
-
Medical Cold Compress Packaging Bag
-
Single-Use Medical Mask Packaging Bags
-
Custom Flat Window Bone Bag For Medical Mask Packaging
-
Self Sealing Bag For Medical Shoe Cover
Transcription printing is the simplest form of perforated printing and began in the late 19th century. This type of printing is done on specially made wax paper, which is made into a wax paper graphic plate by means of a typewriter or an iron pen, on which the wax paper plate is printed with an ink roller, and the desired printing effect is obtained on the substrate. In hole plate printing, the most widely used is screen printing.
Screen printing is the silk fabric, synthetic fabric or metal screen taut on the screen frame, the use of hand engraved lacquer film or photochemical plate making methods to produce screen printing plates. Modern screen printing technology, is the use of light-sensitive materials through the photographic plate making method to produce screen printing plates (so that the screen printing plate on the graphic part of the screen hole for the through-hole, while the non-graphic part of the screen hole is blocked) oil paintings, prints, posters, business cards, framed covers, commodity packaging, commodity signs, printed and dyed textiles, glass and metal, and other flat carriers.
Screen printing refers to the use of a screen as a plate base and the production of a screen printing plate with graphics by means of photographic plate making. Screen printing consists of five main elements: the screen printing plate, the squeegee, the ink, the printing table and the substrate. Screen printing is carried out using the basic principle that the graphic part of the screen plate is permeable to ink and the non-graphic part of the screen is not permeable to ink. The ink is poured into the screen plate at one end of the printing process, and the squeegee is used to apply a certain pressure to the ink part of the screen plate, while moving at a constant speed towards the other end of the screen plate, and the ink is squeezed from the screen holes of the graphic part to the substrate in the movement.
Direct Plate Making Method
- Plate Making Method: The method of direct plate making is in the plate making first coated with photosensitive material wrist film base photosensitive film face up flat on the workbench surface, the taut wrist screen frame flat on the film base, and then in the frame into the photosensitive paste and soft squeegee pressure coating, after drying fully uncovered plastic film base, attached to the photosensitive film wrist screen can be used for sunburning, by the development, drying on the production of screen printing screen plate.
- Process Flow: has been taut screen – degreasing – drying – stripping the film base – exposure –Developing – Drying – Repairing – Sealing
Indirect Plate Making Method
Indirect plate making is the way the indirect film is first exposed, hardened with 1.2% H2O2 and then developed with warm water, dried and made into a peelable graphic negative, plate making will be the graphic negative film surface and taut screen, by squeezing the film and wet screen paste solid, uncover the film base, dry with the wind to make screen printing plate. Process flow.
- It has been taut screen – degreasing – drying
- Indirect film – exposure – hardening – development1and2 – lamination – blowing dry – plate repair – sealing the network
- Straight between the mixed plate making method: the first photopolymer layer of water, alcohol or photopolymer sticky on the screen frame, after hot air drying, remove the photographic film base, and then the sun, the development process is made into a screen plate.
- Not subject to the size and shape of the substrate: general printing, only on a flat surface, and screen printing can not only be printed on a flat surface can also be printed on special shapes such as spherical surfaces on the surface, there are shapes of things can be screen printed to carry out.
- Soft printing pressure on the plate is small, and the screen is soft and flexible.
- Strong ink coverage, pure white printing on all black paper, strong three-dimensional sense.
- Suitable for all types of inks
- High spin resistance. The gloss of the print remains unchanged. (Neither temperature nor sunlight has any effect). This makes it possible to print some self-adhesives without additional processes such as laminating.
- Flexible and varied printing methods
- Easy plate making, cheap and easy to master technology
- Strong adhesion
- Can be screen printed by hand or by machine
- Suitable for long-term display and expressive outdoor advertising
Printing Adaptability
The Strong Sense Of Three-Dimensionality
High Lightfastness
Large Printing Area
Manual printing means that from the renewal of the paper to the receipt of the paper, the printing plate is moved up and down, and the scraper is scraped and printed by hand.
Mechanical printing refers to the printing process is completed by mechanical action. Which is divided into semi-automatic and fully automatic printing, semi-automatic refers to the substrate into and out of the manual operation, printing by mechanical completion; fully automatic refers to the entire printing process are completed by machinery.
There is also a fast and simple curved screen printing screen printing method live surface screen printing, that is, the screen layout is removed directly on the substrate surface for printing. Using the live surface screen printing method, a large number of processing prints can be printed, such as latex plastic buckets, pure water buckets, washbasins, hot water bottles, cups, bowls, plates and other products. At the same time using this method can be printed on cars with sign characters, and also on shaped planes.
The production of a live surface screen plate: first dry and repair the photographic version of the text sensitively, then take it off and cut it to size. And in the two ends of the screen plate with wood or aluminium, etc. as a skeleton with adhesive tape tightly fixed, but also can be used to sticky glue directly fixed, so that the required live surface screen plate can be made. Live surface screen operation method: according to the substrate selection of different printing materials for deployment: first of all, the choice of plate and plate, the ink will be deployed, then, one person holding a live surface screen plate with both hands, the printed part of the substrate tightly on the surface, the other person with a squeegee in the ink transfer board evenly dipped in the squeegee on the mouth surface, then, the squeegee in the ink transfer board evenly placed on the page for uniform scraping.
If the printed graphic area is too large, the ink can be poured on the layout according to the situation, but do not let the ink flow out of the substrate. Note that the deployment of the ink is not too thin, not too dry, dry and wet is good. Small area printing, printing, can be operated by one person, the method is to live surface version of one end with packaging tape on the substrate machine required position, and then, with the other hand to pull the printing plate tightly against the substrate, you can carry out printing. Start note: must be according to the direction of the sticky tape end of the lighter start, if two people operate the start of the plate advertising is also the same, using this method of printing, with easy to operate, the requirements of the substrate flexible, can be large can be small, the number can be more or less, with the advantages of low cost energy savings.
Screen printing is not only adapted to general paper printing, but also to a very wide range of adaptations. Examples include ceramics, glass, printed circuit boards, etc. Depending on the texture of the substrate, the printing is different, although there is an inseparable intrinsic link between the various series, but because the substrate material is different (i.e. different chemical and physical properties), each has its own special characteristics. Therefore, people are usually divided into different substrates: paper printing, plastic printing, ceramic printing, glass printing, circuit board printing, metal printing, textile printing and other major categories. This creates a relatively independent printing system of its own. Screen printing, as a wide range of applications, can be divided according to the different substrates: fabric printing, plastic printing, metal printing, ceramic printing, glass printing, electronic product printing, lottery screen printing, electric decorative advertising board screen printing, metal advertising board screen printing, stainless steel products screen printing, light reflective body screen printing, screen transfer printing electrochemical aluminium, screen printing prints and lacquer screen printing, etc.
Fabric Printing
Paint Direct Printing
Silk Printing
Knitted Lingerie Printing
Drawn And Dyed Printing
Special Printing
Silk Screen Printing
Woolen Fabric Printing
Flat Velvet Printing
Foam Printing
Flocking Printing
Transfer Printing
Everything you need to know to make an informed decision about what poly bag or plastic film product is right for your application. We share information, tips and things we've learned from our years in the plastic bags manufacturing industry.
-
The Advantages Of High-Density Polypropylene Container Bags
-
Unveiling the Enduring Longevity of Ton Bags
-
Understanding the Causes of Uneven Surfaces in Ton Bags
-
Exploring the Art of Sewing Container Bags: Techniques, Methods, and Creativity
-
Precision Spun Musical Drum Kit Packaging
-
What Is Molded Pulp? An In-Depth Exploration of Eco-Friendly Packaging Solutions
-
The Main Role Of Sealing Tape
-
How To Make Plastic Bags Look More Beautiful?
Chaozhou Wonder Plastic Inc is a professional company dedicated to the research and development, production and sales of industrial packaging plastic bags and food packaging plastic bags. Established in 2002, the company is located in the new area of Anbu Town, Chaozhou City, Guangdong Province, with superior geographical location and convenient transportation.
Wonder Plastic has a professional management elite team with a group of high quality talents in R&D, production, quality management and marketing. Since its inception, Wonder Plastic has become a reliable partner for new and old friends in the industry. The company's plastic bags are made of PP, PE, PO, OPP, PPE, CPE, PVC, POF and other materials. Our products are widely used in many fields such as hardware, plastic, toys, crafts, electronics, garments, ornaments, materials, chemicals, textiles, etc. We can design and produce all kinds of packaging bags according to customers' requirements.
The company's existing plant area of nearly 8000 square meters, the existing equipment: 15 sets of film blowing machine, 22 sets of bag cutting machine, offset printing machine 5 sets, eight-colour computer high-speed copper printing machine 1 set, high-frequency wave voltage machine 20 sets, punching machine 4 sets, these equipment can be made for you to produce a variety of industrial packaging plastic bags, a one-stop production to reduce production costs, exquisite printing is the icing on the cake for your products!
Quality is the basis of our factory, quality and reasonable price make us stand in the fierce competition today, the company to high-quality products to meet the promise, to quality in return for care. We warmly welcome your visit and guidance!
Place your order, request a quote, or send us a message with any questions you might have. We help you avoid the pitfalls to deliver the quality and value your poly bag need, on-time and on-budget.