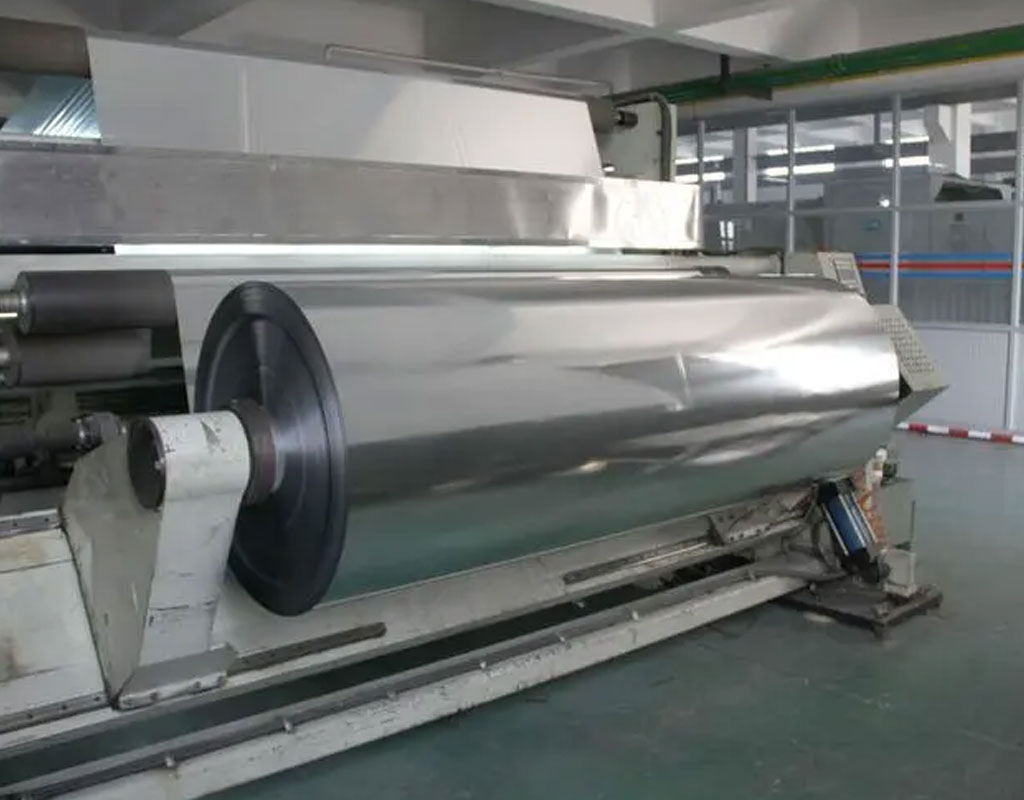
VMPET&VMCPP Suppliers
The aluminised film is a bright metallic coloured film formed by evaporating high purity aluminium wire into a gaseous state at high temperatures (1100-1200°C) through a vacuum aluminising process, after which the gaseous aluminium molecules precipitate onto the surface of the plastic film as it passes through the vacuum evaporation chamber. Aluminised film has both the characteristics of plastic film and metal. The aluminium coating on the surface of the film serves to shade the light and protect it from UV radiation, extending the shelf life of the contents. As a result, aluminised films are widely used in composite packaging, mainly in dry and puffed food packaging such as biscuits, as well as in the outer packaging of some pharmaceuticals and cosmetics. The most used aluminised films are polyester aluminised films (VMPET) and CPP aluminised films (VMCPP).
Wonder Plastic is a ISO 9001:2015 certified supplier of aluminized film. Specifications of aluminized film include 0.002 in. to 0.125 in. thickness & 10 in. to 48 in. width. Aluminized films are available with various finishes, colors & alloys including 1085, 5005, 5657 H19, H34, H25 & H262 grade alloys. No matter what you’re looking for, we can accommodate nearly any specifications to deliver the plastic film or tubing that best suits your application.
-
PE Biodegradable Material PET Poop Bags
-
Transparent Flat Self-Adhesive PE Packaging Bags
-
3-5 Years Old Children’s Socks Packaging Bag
-
PE Organ Shape Bag For Textile Products
-
PE Organ Shape Bag For Clothing
-
Packaging Bag For PET Grooming Glove
-
Medical Packaging Bag For Disposable Respirator
-
Packaging Bag For KN95 Protective Mask
-
Medical Cold Compress Packaging Bag
-
Single-Use Medical Mask Packaging Bags
-
Custom Flat Window Bone Bag For Medical Mask Packaging
-
Self Sealing Bag For Medical Shoe Cover
Aluminised film is a composite flexible packaging material formed by using a special process to coat the surface of plastic film with a very thin layer of metallic aluminium, of which the most commonly used processing method is vacuum aluminising, which is the melting and evaporation of metallic aluminium under high vacuum through high temperature, so that the aluminium vapour precipitates and builds up on the surface of the plastic film, thus making the surface of the plastic film with a metallic lustre. As it has the characteristics of both plastic film and metal, it is a cheap, beautiful, high performance and practical packaging material.
The most used aluminised films are polyester aluminised films (VMPET) and CPP aluminised films (VMCPP). The role of film surface aluminising is to shade and prevent ultraviolet radiation, which not only extends the shelf life of the contents, but also improves the brightness of the film, replacing aluminium foil to a certain extent, and also has inexpensive, beautiful and better barrier properties, therefore, aluminised films are widely used in composite packaging, and are currently mainly used in dry and puffed food packaging such as biscuits, as well as in the outer packaging of some pharmaceuticals and cosmetics.
- Saves energy and materials and reduces costs.
- Excellent folding resistance and good toughness, few pinholes and cracks, no kneading and cracking, so the barrier to gas, water vapour, odour, light, etc. is improved.
- Excellent metallic lustre with light reflectivity of up to 97%; and can be treated with paint to form coloured films, the decorative effect of which is unlike that of aluminium foil.
- Can be partially aluminised by shielding to obtain any pattern or transparent window to be able to see the contents.
- The aluminised layer has good electrical conductivity and can eliminate the electrostatic effect; its sealing performance is good, especially when packaging powdered products, it will not pollute the sealing part and ensure the sealing performance of the packaging.
- Good adaptability to printing, compounding and other post-processing.
Due to the above characteristics, aluminized film has become a new type of composite film with excellent performance and economic beauty, and has replaced aluminium foil composite materials in many aspects. It is mainly used for vacuum packaging of flavoured foods and agricultural products, as well as for packaging of medicines, cosmetics and cigarettes. In addition, aluminised films are also used in large quantities as foil stamping materials and trademark labelling materials in printing.
BOPET and BOPA films can be directly vapour plated without surface treatment before plating. BOPP, CPP, PE and other non-polar plastic films need to be corona treated or coated with a bonding layer to achieve a surface tension of 38-42 dynes/cm or have good adhesion before vapour plating. For vapour deposition, the rolled film is placed in a vacuum chamber and the chamber is closed for evacuation. When the vacuum reaches a certain level (4×10-4mba or more), the evaporation boat will be heated up to 1300℃~1400℃, and then the aluminium wire with 99.9% purity will be continuously sent to the evaporation boat. Adjust the unwinding speed, winding speed, wire feed speed and evaporation volume, open the cooling source, so that the aluminium wire melts and evaporates continuously on the evaporation boat, thus forming a bright aluminium layer after cooling on the moving film surface that is the aluminium-plated film.
The Principle Of Vacuum Vapour Deposition
The coated film substrate (cylinder) is mounted in a vacuum vapour deposition machine and vacuumed with a vacuum pump to achieve a vacuum of 1.3 x 10-2 to 1.3 x 10-3 Pa in the coating. The crucible is heated so that the high purity aluminium wire melts and evaporates into gaseous aluminium at a temperature of 1200°C to 1400°C. The gaseous aluminium particles are deposited on the surface of the moving film substrate and reduced by cooling to form a continuous and shiny metallic aluminium layer. The thickness of the aluminium layer is controlled by controlling the evaporation rate of the aluminium metal, the moving speed of the film substrate and the vacuum level of the coating chamber. Vapour deposition method: There are two methods of aluminium vapour deposition on the surface of the substrate: direct vapour deposition method and transfer method.
- Direct vapour deposition method. The substrate is directly vapour deposited on the surface of the substrate through a vacuum coating machine to form an aluminium-plated film. The direct vapour deposition method has high requirements on the substrate, especially to form a bright surface metal film, the substrate must be required to have a good surface smoothness. If the surface of the paper is rough, direct vapour deposition requires a surface coating before the aluminium plating is applied. In addition, the substrate must have a low level of volatiles during the vapour deposition process. Therefore, the direct vapour deposition method has greater limitations on the substrate, it is mainly suitable for vapour deposition of plastic films, can also be used for paper vapour deposition, but the quality of the paper requires high and has a certain limit on the quantity of paper.
- Transfer method. It is the transfer of the metallic aluminium layer to the surface of the substrate with the help of a carrier film (vacuum aluminised film) to form an aluminised film. The transfer method is a new process developed on the basis of the direct vapour plating method, which overcomes the limitations of the substrate requirements of the direct vapour plating method and is particularly suitable for aluminium plating on various kinds of paper and cardboard, and can also be used for the aluminium plating of plastic films. The transfer method has been applied abroad to the aluminising of cloth, fibres, leather and other substrates. China mainly uses the transfer method to produce aluminised paper.
Aluminised Film Production Process
The Adhesion Testing Of Aluminized Film
Everything you need to know to make an informed decision about what poly bag or plastic film product is right for your application. We share information, tips and things we've learned from our years in the plastic bags manufacturing industry.
-
The Advantages Of High-Density Polypropylene Container Bags
-
Unveiling the Enduring Longevity of Ton Bags
-
Understanding the Causes of Uneven Surfaces in Ton Bags
-
Exploring the Art of Sewing Container Bags: Techniques, Methods, and Creativity
-
Precision Spun Musical Drum Kit Packaging
-
What Is Molded Pulp? An In-Depth Exploration of Eco-Friendly Packaging Solutions
-
The Main Role Of Sealing Tape
-
How To Make Plastic Bags Look More Beautiful?
Chaozhou Wonder Plastic Inc is a professional company dedicated to the research and development, production and sales of industrial packaging plastic bags and food packaging plastic bags. Established in 2002, the company is located in the new area of Anbu Town, Chaozhou City, Guangdong Province, with superior geographical location and convenient transportation.
Wonder Plastic has a professional management elite team with a group of high quality talents in R&D, production, quality management and marketing. Since its inception, Wonder Plastic has become a reliable partner for new and old friends in the industry. The company's plastic bags are made of PP, PE, PO, OPP, PPE, CPE, PVC, POF and other materials. Our products are widely used in many fields such as hardware, plastic, toys, crafts, electronics, garments, ornaments, materials, chemicals, textiles, etc. We can design and produce all kinds of packaging bags according to customers' requirements.
The company's existing plant area of nearly 8000 square meters, the existing equipment: 15 sets of film blowing machine, 22 sets of bag cutting machine, offset printing machine 5 sets, eight-colour computer high-speed copper printing machine 1 set, high-frequency wave voltage machine 20 sets, punching machine 4 sets, these equipment can be made for you to produce a variety of industrial packaging plastic bags, a one-stop production to reduce production costs, exquisite printing is the icing on the cake for your products!
Quality is the basis of our factory, quality and reasonable price make us stand in the fierce competition today, the company to high-quality products to meet the promise, to quality in return for care. We warmly welcome your visit and guidance!
Place your order, request a quote, or send us a message with any questions you might have. We help you avoid the pitfalls to deliver the quality and value your poly bag need, on-time and on-budget.