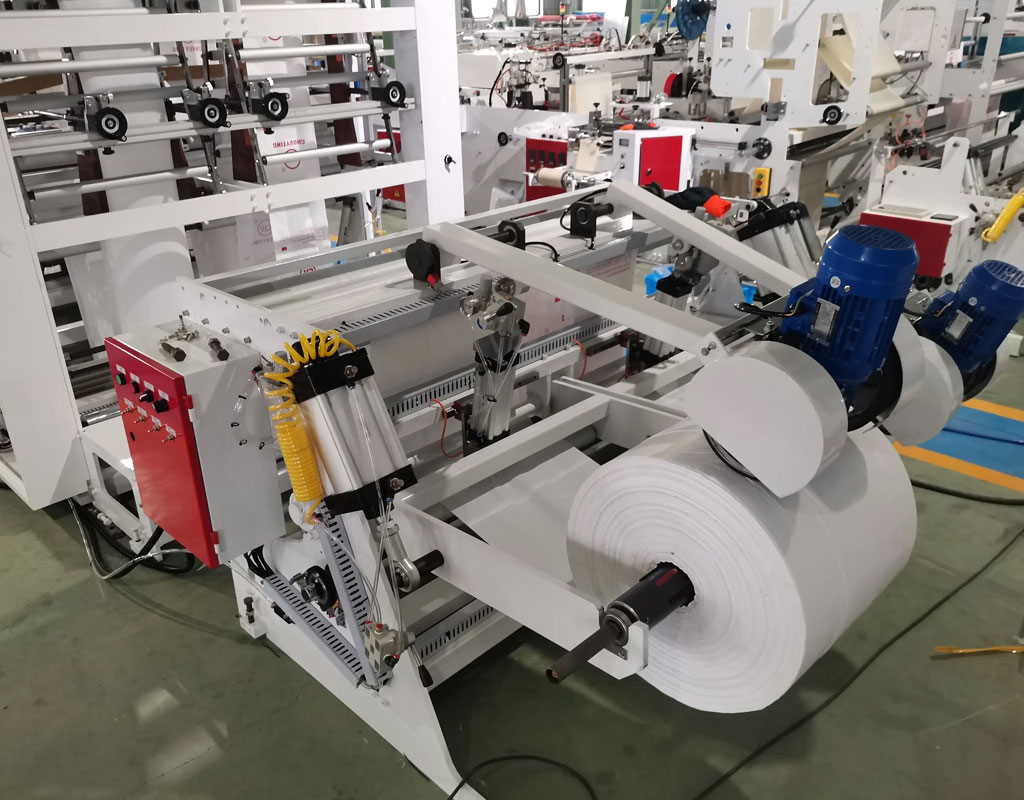
Plastic Film Manufacturer
Standard And Custom Plastic Film Manufacturer of Co-Extruded Plastic Films available in materials including nylon 6 and 66, acetal, HDPE, LDPE and polypropylene. Extruded plastic films are available in standard colors with thickness ranging from 0.010 in. to 0.187 in., untrimmed width up to 38 in., slit width of 0.5 in. and core sizes of 3 in. and 8 in. Extruded polyolefin films are available in width up to 38 in. and nylon and acetal films are available in width up to 20 in.
Plastic films can be customized for core sizes, matching colors and materials upon request . Made from low, medium or high-density polyethylene and polypropylene. Available in 1 to 108 in. width, 300 to 15,000 ft. length, vertical or horizontal direction perforations and clear, white, blue, black or white colors.
Moreover, they offers a comprehensive range(printing and designs) of products to suit any custom packaging application
Also, with our plastic film, packaging are not a problem. From single wound and centerfold sheeting to polyethylene tubing, we can develop the film or tubing you need for parts packing, overwrap and more. If you need something that is not listed, you can get in touch with us. Our team expert will assist you with your needs and your order ships in as little as 2-3 weeks.
-
PE Biodegradable Material PET Poop Bags
-
Transparent Flat Self-Adhesive PE Packaging Bags
-
3-5 Years Old Children’s Socks Packaging Bag
-
PE Organ Shape Bag For Textile Products
-
PE Organ Shape Bag For Clothing
-
Packaging Bag For PET Grooming Glove
-
Medical Packaging Bag For Disposable Respirator
-
Packaging Bag For KN95 Protective Mask
-
Medical Cold Compress Packaging Bag
-
Single-Use Medical Mask Packaging Bags
-
Custom Flat Window Bone Bag For Medical Mask Packaging
-
Self Sealing Bag For Medical Shoe Cover
Films made from polyvinyl chloride, polyethylene, polypropylene, polystyrene and other resins are used for packaging, as well as for laminating layers. The share of plastic packaging and plastic packaging products in the market is increasing, especially the composite plastic flexible packaging, has been widely used in food, medicine, chemical industry and other fields, among which the largest proportion of food packaging, such as beverage packaging, frozen food packaging, steamed food packaging, fast food packaging, etc., these products have brought great convenience to people’s lives.
Plastic films are most widely used in the packaging sector. Plastic films can be used for food packaging, packaging for electrical products, packaging for daily necessities, clothing packaging and so on. One thing they have in common is that plastic films are printed in colour, and as food packaging they are also subjected to multilayer lamination or vacuum aluminising processes. Therefore, the surface free energy of plastic film is required to be high and the wet tension to be high, in order to facilitate the solid bonding of printing ink, adhesive or aluminising layer with the plastic film; in the process of plastic film production and high-speed packaging, the film surface is required to have certain friction properties to prevent film adhesion or slippage; when used for electrical and electronic products packaging, the film is required to have certain anti-static properties, etc.
The Surface Tension Of Plastic Films
The Surface Treatment Methods Of Plastic Films
The Basic Principle Of The Corona Treatment Method
Commonly used plastic films are polyethylene (PE), polyvinyl chloride (PVC), polystyrene (PS), polyester film (PET), polypropylene (PP), nylon and so on. The performance of various plastic films varies, as does the ease of printing, and their use as packaging materials.
- Polyethylene film is a colourless, tasteless, odourless, translucent, non-toxic insulating material, used in large quantities as packaging bags; food bags, but also to make a variety of containers. It is an inert material, so it is more difficult to print and must be treated to produce better results.
- Polyvinyl chloride film has better light resistance, ageing resistance and better tear resistance, it is breathable and is a clean, colourless, transparent film, generally with plasticisers, it is soluble in solvents such as acetone and cyclohexanone. Therefore, it can be printed with inks made from polyvinyl chloride resins. It is suitable for packaging bags, book covers, etc.
- Polystyrene film is a soft and tough film, clean, colourless and transparent, without plasticisers, the film layer is always soft, resistant to freezing, stored without ageing, printed with oxidation polymerisation of synthetic linker ink, which can make the print fastness better.
- Polyester film is colourless, transparent, moisture resistant, impermeable, soft, strong, resistant to acid and alkali oil esters and solvents, to high and low temperatures are not afraid of the material, after the EDM treatment, the ink has a relatively good surface fastness. Used for packaging and composite materials.
- Polypropylene film has a good gloss and good transparency, is resistant to heat, acid and alkali, solvents, friction, tearing and can breathe, and cannot be heat sealed below 160°C.
- Nylon film is stronger than polyethylene film, odourless, non-toxic, impervious to bacteria, resistant to oil, esters, boiling water and most solvents, and is generally used for load-bearing, wear-resistant packaging, as well as for steaming packaging (reheating of food), which can be printed without surface treatment.
- Polyethylene molecule basically without polar groups, is a non-polar printing high points in, polypropylene molecules, each structural unit contains a methyl group, which is divided into weak polar groups, basically also belongs to the non-polar polymer, therefore, they are poor affinity to the ink, so before printing in the printing before the treatment to get a satisfactory print.
- Most of the treatment methods are through oxidation, so that the polarity increases and the surface structure changes. The specific treatment methods are electrical discharge (commonly known as corona, electric spark) method, flame method, ultraviolet radiation method, acid (sulphuric acid, chromic acid) treatment method and several other methods. The electrical discharge method is relatively simple and popular.