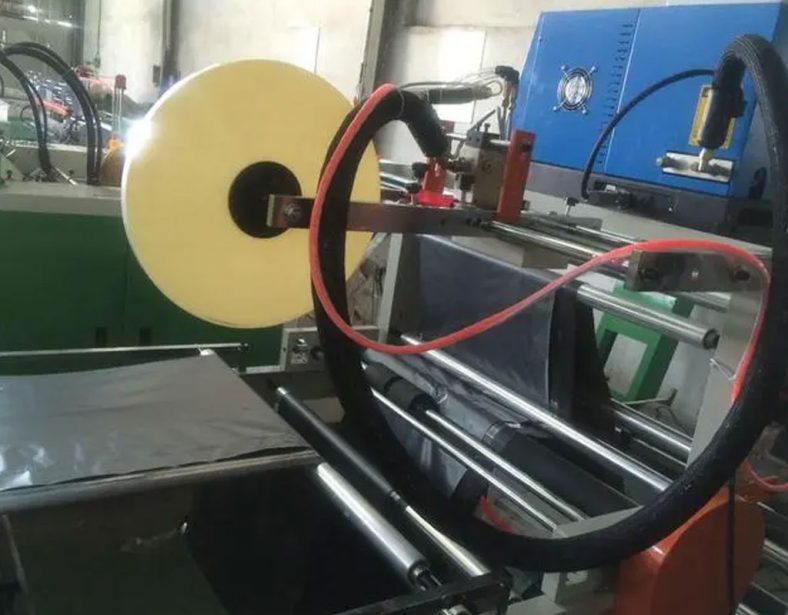
Poly bags are widely used in a variety of industries due to their low cost, versatility, and durability. They are used to package a wide range of products, including food, clothing, and household goods.
Here at Wonder Plastic, we use a blown-film extrusion process to manufacture the plastic that makes poly bags. Once the plastic is formed and wound on a roll, our poly bag manufacturing machines seal and cut bags according to each client’s custom poly bag specifications. Here’s a closer look at how poly bags are made.
How Poly Bags Are Made
Poly bags, also known as polyethylene bags, are made through a process called blown film extrusion. Here’s a general overview of how poly bags are made:
- Raw polyethylene resin is fed into a hopper and melted down in an extruder.
- The melted polyethylene is then forced through a circular die to form a tube of molten polyethylene.
- Air is blown into the center of the tube to inflate it and give it the desired shape and thickness.
- The inflated tube is cooled by passing it through a series of cooling rolls.
- The cooled tube is cut into bags of the desired size using a rotary cutting machine.
- The bags are then sealed using heat or ultrasonic energy, depending on the type of bag being made.
- The finished bags are then inspected for quality and packed for distribution.
The Blown-Film Extrusion Process
The blown-film extrusion process is used to manufacture a wide range of products, including poly bags, plastic films, and packaging materials. It is a continuous process that involves melting down raw polyethylene resin and extruding it through a circular die to form a tube of molten polyethylene.Here’s a more detailed overview of the blown-film extrusion process:
- Raw polyethylene resin is fed into a hopper and melted down in an extruder. The extruder consists of a barrel, a screw, and a motor. The barrel is heated to a high temperature to melt the resin, and the screw helps to melt and mix the resin as it moves through the barrel.
- The melted polyethylene is then forced through a circular die to form a tube of molten polyethylene. The die determines the shape and thickness of the final product.
- Air is blown into the center of the tube through a small hole in the die. This inflates the tube and gives it the desired shape and thickness.
- The inflated tube is cooled by passing it through a series of cooling rolls. This helps the tube to solidify and maintain its shape.
- The cooled tube is cut into sheets or rolls of the desired width using a rotary cutting machine.
- The sheets or rolls are then processed further, depending on the specific product being made. For example, poly bags are typically sealed using heat or ultrasonic energy.
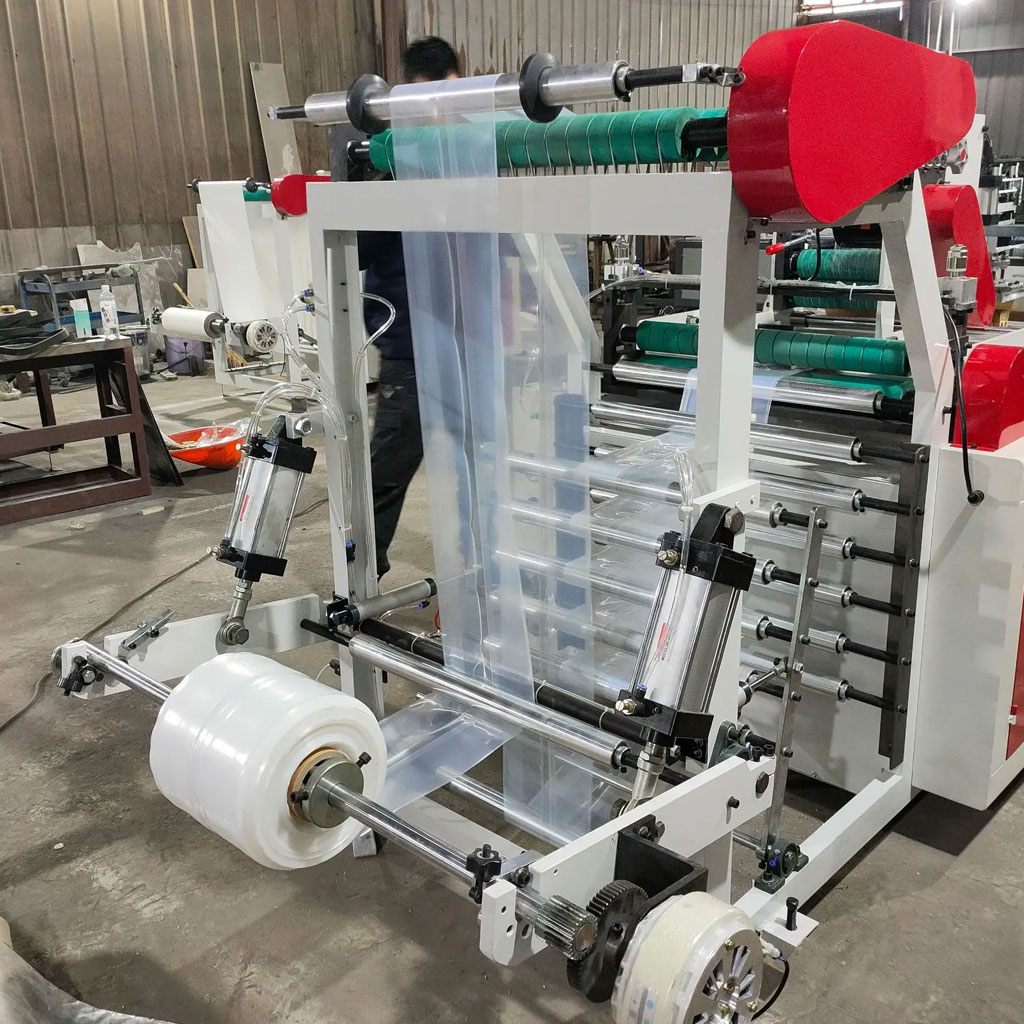
The blown-film extrusion process is highly efficient and allows for the production of a wide range of products with different shapes, sizes, and properties. It is also relatively easy to control and customize, making it a popular choice for manufacturers.
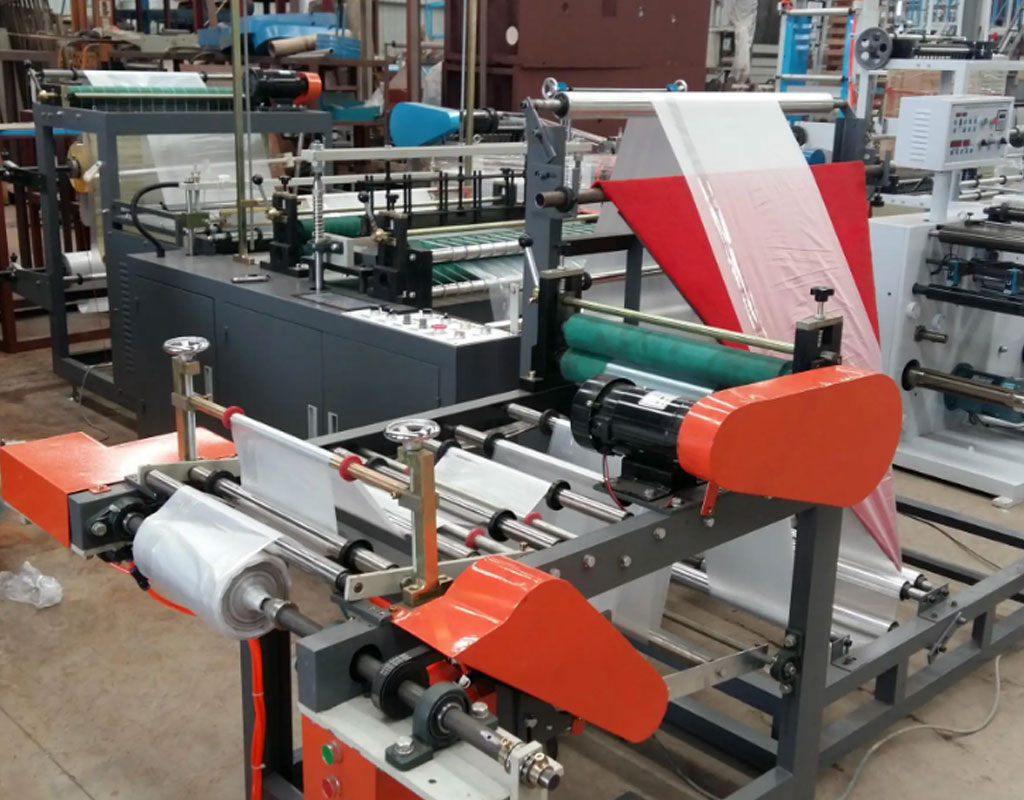
How To Making Poly Bags from Plastic Rolls
To make poly bags from plastic rolls, you will need the following materials and equipment:
- Plastic rolls (polyethylene or other suitable plastic)
- Cutting machine (e.g., rotary cutter, slitter, or guillotine cutter)
- Heat sealer or ultrasonic sealer
- Optional: printing equipment (e.g., flexographic printer or inkjet printer)
Here’s a general overview of the process:
- Start by obtaining rolls of plastic film, such as polyethylene. The rolls should be of the desired thickness and size for the poly bags you want to make.
- Cut the plastic rolls into sheets of the desired size using a cutting machine. You can use a rotary cutter, slitter, or guillotine cutter, depending on the size and shape of the bags you want to make.
- Optional: If you want to print on the bags, you can use printing equipment to apply the desired graphics or text onto the sheets of plastic.
- Fold the sheets of plastic into the desired shape and size for the poly bags.
- Use a heat sealer or ultrasonic sealer to seal the edges of the bags, creating a secure and airtight seal.
- Inspect the finished poly bags for quality and packaging them for distribution.
It is important to follow proper safety protocols when handling the cutting and sealing equipment to prevent accidents and injuries. You may also need to follow local regulations and guidelines for the production of poly bags.