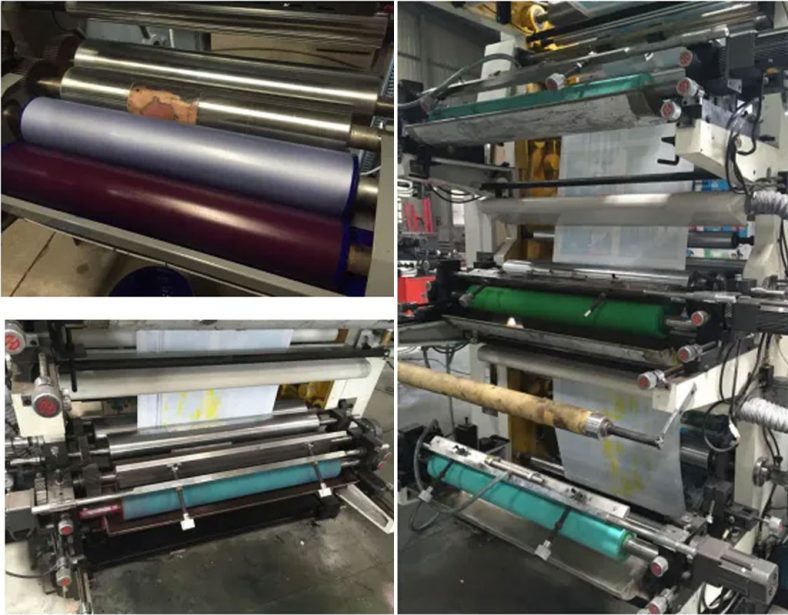
Custom Flexographic Printing
Flexographic printing is a printing method that uses a flexible plate and passes the ink through anilox rollers to apply the print. In flexography, the printing plate is generally a photopolymer plate with a thickness of 1-5mm. The inks are divided into three main categories, namely water-based inks, alcohol-soluble inks and UV inks. As the inks used in flexographic printing are in line with the green environment, they have been used in large quantities for food packaging printing and have a bright future. Flexographic printing is a type of letterpress printing.Wonder Plastic is a Lean manufacturing capable custom manufacturer of flexographic printing. No matter what you’re looking for, we can accommodate nearly any specifications to deliver the plastic film or bags that best suits your application.
-
PE Biodegradable Material PET Poop Bags
-
Transparent Flat Self-Adhesive PE Packaging Bags
-
3-5 Years Old Children’s Socks Packaging Bag
-
PE Organ Shape Bag For Textile Products
-
PE Organ Shape Bag For Clothing
-
Packaging Bag For PET Grooming Glove
-
Medical Packaging Bag For Disposable Respirator
-
Packaging Bag For KN95 Protective Mask
-
Medical Cold Compress Packaging Bag
-
Single-Use Medical Mask Packaging Bags
-
Custom Flat Window Bone Bag For Medical Mask Packaging
-
Self Sealing Bag For Medical Shoe Cover
Flexographic printing, offset printing, gravure printing and screen printing are the four most common printing methods in the world, they have their own characteristics, each with its own characteristics. In Europe and the United States and other countries with a developed printing industry, flexographic printing is developing rapidly, packaging printing has changed from gravure and offset printing to flexographic printing, in about 70% of packaging materials using flexographic printing.
With the development of the commodity economy and people’s living standards continue to improve, the packaging printing industry is also moving towards high-grade, fine, multi-species direction. However, offset printing and gravure printing accounted for a considerable market share, while the start of flexographic printing is relatively late, especially in the printing of high-grade products. With the continuous application of new technologies, flexographic printing has made great progress, product quality directly after the offset and gravure printing, with a fairly strong market competitiveness.
Compared to gravure, offset and traditional letterpress, flexographic printing has its own distinctive features:
- Low Cost:Compared to gravure presses and offset presses of the same colour group, the price of a flexographic press is much lower. In addition, the flexographic printing machine combines printing, die-cutting and varnishing processes in a single process, so that multiple processes can be completed in a single operation without the need to purchase additional post-processing equipment.
- Simple Equipment:The simple structure of the machine makes it easy and convenient to operate.
- High Efficiency:Flexo printing is done on rolls, which not only enables double-sided printing of the substrate, but also enables inline varnishing (or laminating), foil stamping, die-cutting, scrap removal and rewinding. This greatly shortens the production cycle, saves manpower, material and financial resources, reduces production costs and increases economic efficiency.
- Wide Range:A wide range of materials can be printed, such as paper, plastic film, aluminium foil, self-adhesive paper, etc.
- Good Quality:The print quality is good, the printing accuracy can reach 150 lines/inch, and the print is rich in layers, vivid colours and good visual effects, especially suitable for packaging printing requirements.
- Environmentally Friendly:New water-based and solvent-based inks are used, which are non-toxic and non-polluting and fully meet the requirements of green environmental protection and also meet the requirements of food packaging.
- Good Efficiency:Flexographic printing presses use web-type materials and can be used inline with many post-press devices, greatly reducing cycle times. The cost of flexo printing is only 10%-20% of gravure printing, ink consumption is 1/3 less than gravure printing, power saving is 40% and the scrap rate is only 1%-2%, lower than gravure and offset printing, thus reducing production costs.
The two main steps are plate making and printing
- Plate Making:original – film (positive negative) – back exposure – main exposure – development and processing — drying – post-processing – post-exposure – mounting the plate for printing.
- Flexographic Printing, which combines the characteristics of lead, lithographic and gravure printing processes, such as: the use of highly flexible letterpress plates, the use of metal anilox rollers with holes in the quantitative ink supply, printing ink is good fluidity, low viscosity of fast-drying solvent or water-based ink, printing quality can be compared with lithographic printing. It is suitable for printing all kinds of paper, plastic film, metal film, self-adhesive and many other printing materials. Flexographic printing presses, thanks to the short ink path of the metal anilox roller ink supply system, the ink quantity is easy to control and the automation procedure is high, therefore, the operation technology of printing is simpler than letterpress and litho printing.
The Anilox Rollers Of Flexographic Printing
The Ink Of Flexographic Printing
The Ink Scraper Of Flexographic Printing
According to the original and the customer’s requirements, choose the appropriate number of colours, colour sequence, width and the corresponding plate rollers (number of teeth, number of screens, etc.).
Many of the originals for flexographic printing are transferred from offset printing, and there is a great difference between the two printing processes. Therefore, it is not possible to copy the offset printing process (especially the colour separation process), but to handle the originals according to the characteristics of the flexographic printing process itself, combined with the performance of the company’s flexographic printing presses, and to coordinate with the customer.The printing pressure, printing speed and the adjustment of the tension of each part must be appropriate.
Because flexo plates are made up of a hard polyester base and a highly elastic photographic material, their most obvious characteristic is that they are flexible. In the printing process and the need to apply a certain amount of printing pressure, despite the use of light pressure printing in flexo printing, but the slight change in printing pressure can also cause changes in colour and level of reproduction, resulting in the expansion of the image dot on the print. Moreover, a high printing pressure results in severe dot gain.
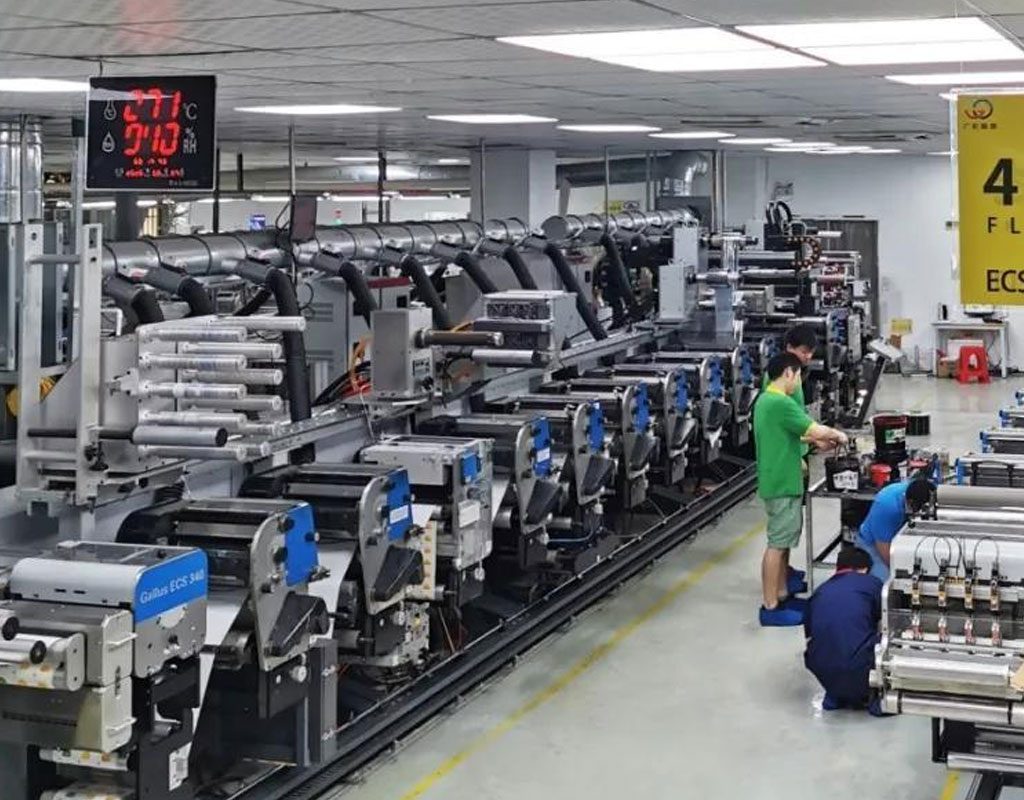
Printing speed should be combined with the specific production situation to determine the machine start from a low speed, adjust the position of each colour group printing plate cylinder, to achieve registration and then gradually increase the speed of the machine, and with the drying properties of the ink to adapt, but also pay attention to the machine speed can not be too fast, to prevent the occurrence of spatter ink, resulting in unnecessary waste, or even affect production.
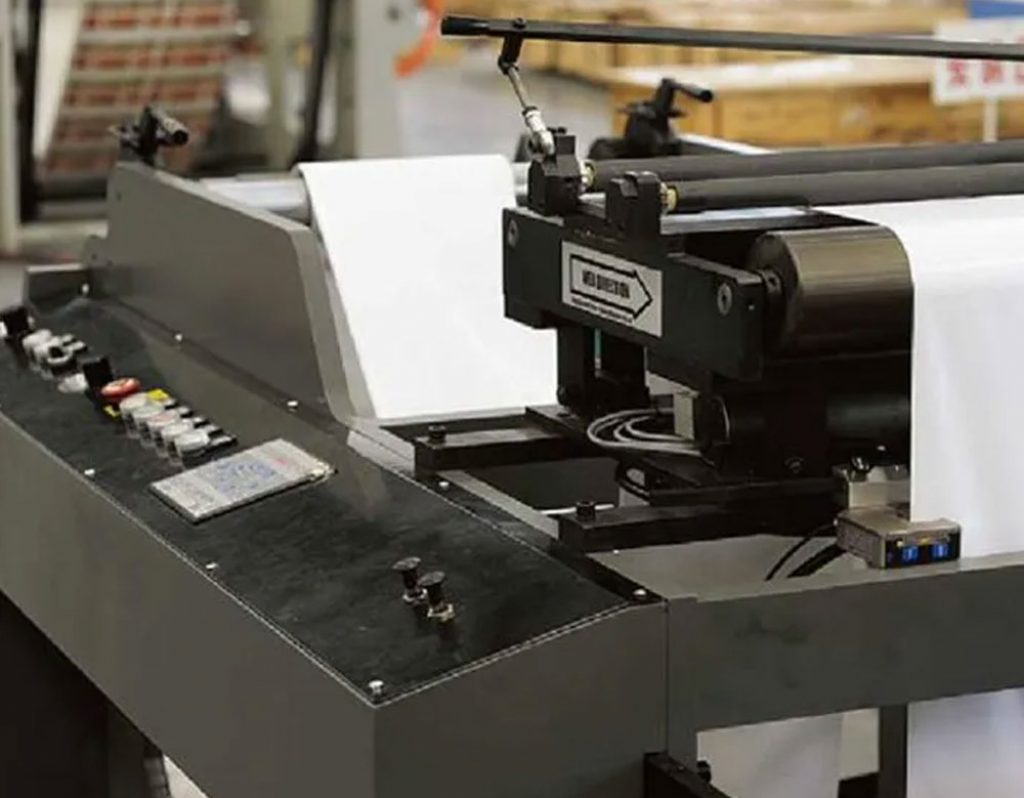
Tension adjustment and control is very important, if the tension is not appropriate, it will lead to inaccurate printing overlay, skewed material, untidy winding and other failures.During the printing process, the viscosity, PH value and drying performance of the ink should be checked at all times.
For flexo printing ink control, these are the three main aspects. In the production process, due to the evaporation of water and solvents, the performance of the ink becomes unstable, the viscosity rises and the PH value decreases, affecting the printability.
Therefore, in the printing process, every certain time, to add the appropriate amount of PH value stabiliser or the corresponding solvent (to be combined with the specific printing speed and ink drying), to adjust the PH value and viscosity of the ink. At the same time, as flexo is short-station printing, the stroke between the colour and the colour is relatively short, if the solvent in the ink does not dry thoroughly, it will lead to poor colour stacking or sticking.
The Pre-printing Techniques Of Flexographic Printing
The Pre-printing Advantages Of Flexographic Printing
Pre-printing technology has become an important development trend in corrugated carton printing, especially for high-grade fine cartons, including large and heavy cartons, which are more suitable for pre-printing. Surveys show that in the Chinese domestic market, offset printing is still dominant in corrugated carton printing, mainly in the case of single-sided paper; while in the US 70% of corrugated carton printing is pre-printed, of which flexo printing accounts for 3/4, while the other 1/4 is almost taken up by gravure printing, meaning that the rate of offset printing is almost close to zero.According to expert analysis, compared to the “post-printing” process (direct printing) of corrugated boxes, the pre-printing process has unique advantages:
- High-quality coloured cartons can be obtained, keeping the colour consistent.
- The ability to produce large format coloured boxes. Compared to the previous limitations of laminated offset printing and the narrow and medium widths of existing flexo direct printing, pre-printing is capable of producing large format corrugated boxes, reportedly up to 1.7 x 1.7m, with the ability to produce multi-colour printing. Despite the fact that super-wide offset printing machines are gradually beginning to print directly on the corrugated board market, the quality of super-wide offset printing is somewhat limited due to the relative imperfection of the technical process.
- Obtain higher strength corrugated boxes. Because pre-printing is not required after the corrugated board is formed, it can avoid corrugated deformation and weaken the strength of the cardboard; when direct printing is used, it will cause more or less deformation of the cardboard, and as the number of printing increases, the deformation of the corrugated and cardboard becomes larger and larger.
- Higher production efficiency and easier production management. Pre-printing is the printing of webs, its printing speed is higher, although corrugated cardboard after the printing machine can also reach a fairly high speed, but the pre-printing machine adjustment and auxiliary time, scrap rate, failure downtime are to be significantly reduced.
- Adaptation to long-run jobs.Due to the increased productivity of pre-press, the ability to adapt to long-run jobs and the automation of corrugated board machines makes the pre-press process more suitable for high-volume, long-run jobs.
In addition, the advantages of the pre-printing process are also manifested in its low printing costs for corrugated boxes and the comparative difficulty of imitation printing, which brings direct production benefits to the company and indirect benefits from brand protection.
Everything you need to know to make an informed decision about what poly bag or plastic film product is right for your application. We share information, tips and things we've learned from our years in the plastic bags manufacturing industry.
-
The Advantages Of High-Density Polypropylene Container Bags
-
Unveiling the Enduring Longevity of Ton Bags
-
Understanding the Causes of Uneven Surfaces in Ton Bags
-
Exploring the Art of Sewing Container Bags: Techniques, Methods, and Creativity
-
Precision Spun Musical Drum Kit Packaging
-
What Is Molded Pulp? An In-Depth Exploration of Eco-Friendly Packaging Solutions
-
The Main Role Of Sealing Tape
-
How To Make Plastic Bags Look More Beautiful?
Chaozhou Wonder Plastic Inc is a professional company dedicated to the research and development, production and sales of industrial packaging plastic bags and food packaging plastic bags. Established in 2002, the company is located in the new area of Anbu Town, Chaozhou City, Guangdong Province, with superior geographical location and convenient transportation.
Wonder Plastic has a professional management elite team with a group of high quality talents in R&D, production, quality management and marketing. Since its inception, Wonder Plastic has become a reliable partner for new and old friends in the industry. The company's plastic bags are made of PP, PE, PO, OPP, PPE, CPE, PVC, POF and other materials. Our products are widely used in many fields such as hardware, plastic, toys, crafts, electronics, garments, ornaments, materials, chemicals, textiles, etc. We can design and produce all kinds of packaging bags according to customers' requirements.
The company's existing plant area of nearly 8000 square meters, the existing equipment: 15 sets of film blowing machine, 22 sets of bag cutting machine, offset printing machine 5 sets, eight-colour computer high-speed copper printing machine 1 set, high-frequency wave voltage machine 20 sets, punching machine 4 sets, these equipment can be made for you to produce a variety of industrial packaging plastic bags, a one-stop production to reduce production costs, exquisite printing is the icing on the cake for your products!
Quality is the basis of our factory, quality and reasonable price make us stand in the fierce competition today, the company to high-quality products to meet the promise, to quality in return for care. We warmly welcome your visit and guidance!
Place your order, request a quote, or send us a message with any questions you might have. We help you avoid the pitfalls to deliver the quality and value your poly bag need, on-time and on-budget.